ORGANIZATIONAL TRANSFORMATION PROGRAMS VIA OPERATIONAL EXCELLENCE PROGRAMS
20/09/2021
Votorantim Group (CEMENT, PULP AND METALS)
Project led by the company’s Board of Directors as part of the company’s Value Generation Strategy, involving the CEOs of all the Group’s Businesses, as well as the formation of a committee of Master Black Belts and Black Belts composed of more than 100 professionals, 100% dedicated to implementing the Program. Seta has trained roughly 1000 professionals since 2004 in the Lean and Six Sigma methodologies in Brazil, Peru, Colombia, the United States and Canada, from Votorantim Cements, Metals (Zinc, Nickel and Aluminum) and Pulp and Paper (Fibria). Material 100% customized to the company’s reality. Approximately 1000 Lean Six Sigma projects have been mentored, bringing a significant financial return with impact corroborated by the finance departments of the Group’s different Businesses. Training of in-house trainers and material developed in English, Portuguese and Spanish. Attending meetings with the Group’s executives and participation in all certification ceremonies. Ensuring that the Program was 100% aligned with the company’s Management model - SGV (Sistema de Gestão Votorantim).
Eurofarma (PHARMACEUTICALS)
Support to the company’s CEO and primary shareholder for implementing the Lean Six Sigma Program, having trained more than 300 employees as Kaizen Leaders, Green Belts, Black Belts and Champions since 2006. More than 250 projects developed with significant financial returns corroborated by the company’s finance department. Material customized to the company’s reality.
Albert Einstein (HOSPITAL)
Work begun in 2008, developing materials customized to the reality of the Hospital. Support to the General Manager of the Albert Einstein Hospital to structure its Management area based on Lean Six Sigma, seeking in-house and external professionals to form the Management team. Green Belt and Black Belt training for the administrative and medical staff, as well as Lean training for the Assistance Group. Over 300 projects developed, aiming to improve the Hospital’s primary operational indicators.
Avon (COSMETICS)
Structuring of an Operational Excellence Board alongside the company’s CEO and VP of HR, also including recruitment and hiring of professionals to form the Board.Work started in 2013. More than 200 professionals trained as Six Sigma Green Belt, Black Belts, Master Black Belts and Champions. Expressive financial gains corroborated by the finance department. Program recognized by Avon Corporate as a benchmark within the group.
Braskem (CHEMICALS)
Project developed since 2006 with the Management area at all of the group’s facilities in Brazil (Camaçari, Maceió, Duque de Caxias, Capuava, Triunfo) and in the USA, for both the Basic Input Unit and for the Polymers area. Training conducted in English and Portuguese, fully aligned with the Management strategy - Braskem Mais. Over 500 professionals trained as Six Sigma Green Belts, Black Belts and Master Black Belts, and in-house instructors trained using material developed, customized and granted by Seta. Participation in Certification events.
OI (TELECOMMUNICATIONS)
Project developed since 2010 with the Management area, training approximately 200 Green Belts, Black Belts and Master Black Belts at the company with financial returns corroborated by the Controller’s Office. Participation in all certification events and relationship with the Organization’s executives, aligned with the organization’s established goals. Development of customized material, granted to the company to be used to train professionals with its own resources.
GVT / Telefônica / Vivo (TELECOMMUNICATIONS)
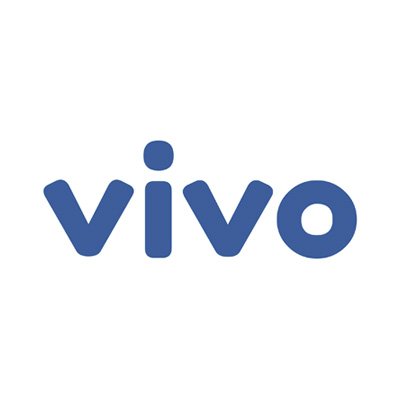
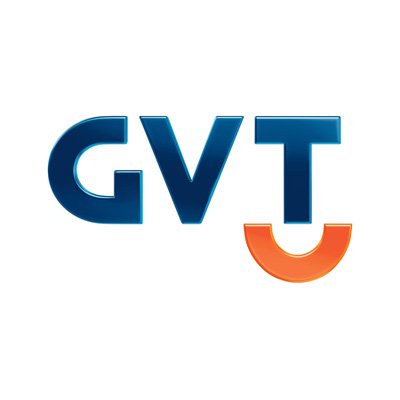
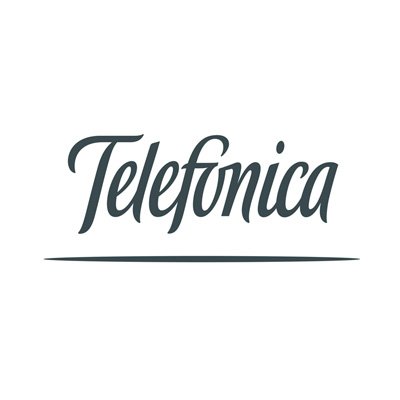
Project developed from 2012 to 2016 with the Board of Directors, training approximately 1000 Yellow Belts, Green Belts, Black Belts and Master Black Belts at the company with significant financial return corroborated by the Controller’s Office. Participation in all certification events and relationship with the Organization’s executives, aligned with the organization’s established goals. Development of customized material, granted to the company to be used to train professionals with its own resources.
Itaú (BANK)
Starting in 2012 Itaú Bank decided to implement a culture of achieving small improvements in the areas by deploying the Lean Office model (Kaizen event). Alongside the Business School, Seta developed a training program to support formation of Kaizen Leaders. The training included leadership skills so that the Kaizen Leader could conduct events effectively with superior results. Over 200 people were trained, who now conduct more than 1000 Kaizen Events every year at the institution.