Since 2004, Seta has been training professionals from large leading companies in the most diverse sectors in Brazil and Worldwide.
Throughout this trajectory, we have become a reference in training and consulting in People Development and Operational Excellence.
Now, you will have access to one of these trainings!
Who we are:
+ 2000 customers in Brazil and worldwide
+ 300,000 people trained
Meet some of these clients:
Learn more about LSS White Belt certification:
In this free training, you will learn about the famous Lean Six Sigma continuous improvement methodology, and you will have access to several quality tools for you to use them in your professional challenges.
You will be able to drive improvements in your corporate environment, in addition to supporting more complex Lean Six Sigma projects, effectively participating as a team member in Yellow, Green and Black Belt projects.
Along this journey, you will learn about the DMAIC model, which aims to increase the productivity and efficiency of processes, reducing waste, and in some cases also bringing financial benefits.
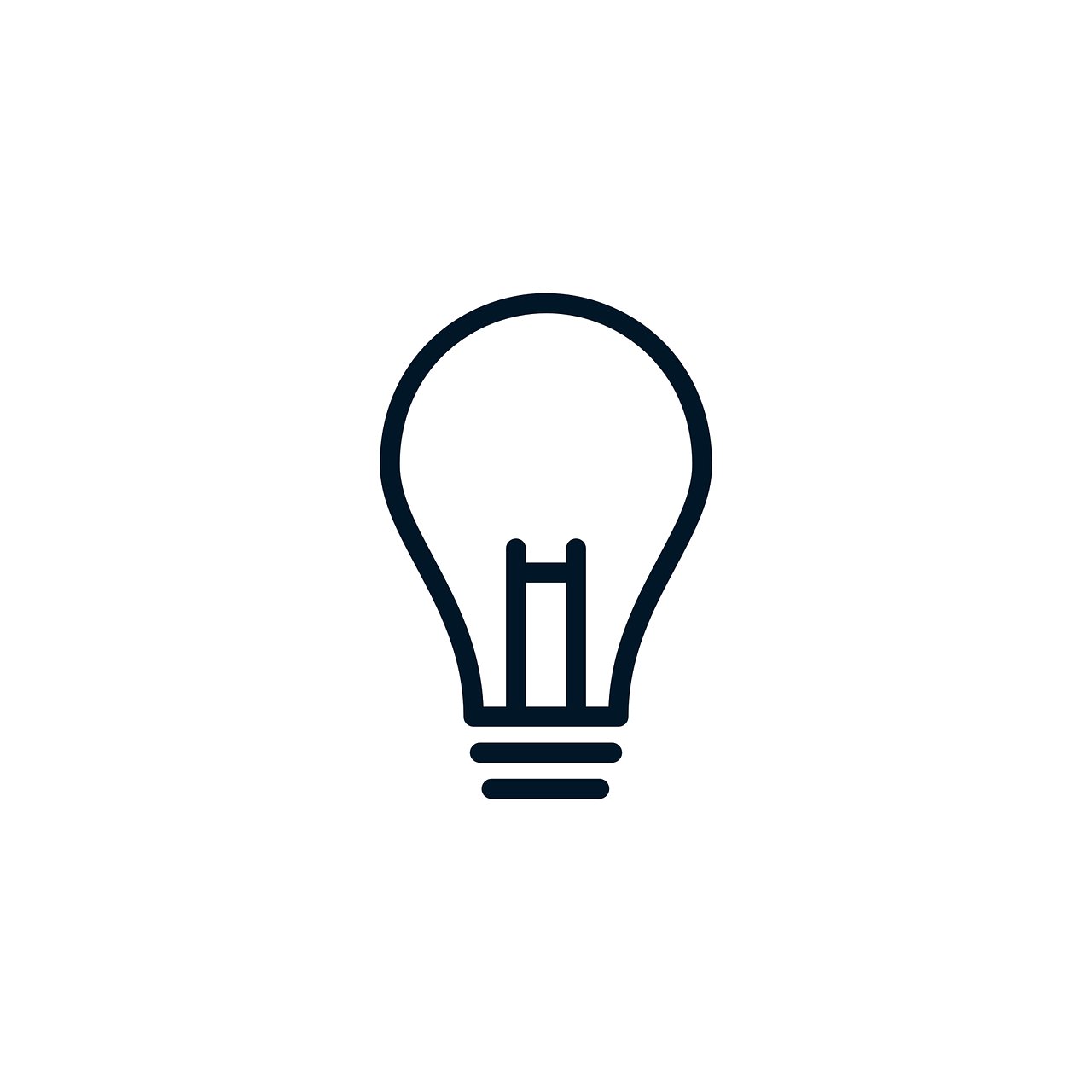
Upon completing the training, you will be certified as an LSS White Belt, the first of the Lean Six Sigma proficiency levels, and will be able to:
• Understand the structure and vocabulary of Lean Six Sigma projects;
• Drive improvements through the application of quality tools;
• Assist teams in applying this methodology in continuous improvement projects.
About the content:
Our training is designed to get straight to the point, helping you to understand in a simplified way the fundamentals of the Lean Six Sigma world. You will have access to 02 hours of content, divided into 07 modules, with access to videos, texts and tool templates to use in your daily life.
Audience and prerequisites:
The certification is intended for professionals who are interested in conducting projects and improvements in their professional environments.
For this training, you will only need a device with internet connection (Computer/Mobile).
Discover our modules:
• Introduction
You’re welcome to the Lean Six Sigma platform and world.
• Definition (Define)
Define the problem that will be worked on among the priorities of the business, in addition, it is at this moment that the work team and the objectives that are expected to be achieved through the application of the methodology are defined.
• Measurement (Measure)
Measuring involves gathering quantitative and qualitative data related to the problem being studied in order to identify potential causes and make future comparisons.
• Analysis (Analyze)
The analysis is the moment to select the main causes and sources of variation of the problem faced. Only then will it be possible to complete the
next steps and create strategies that act directly in solving the root cause of the problem.
• Improvement (Improve)
This is where most actions are taken. At this stage, we define the improvement actions and prioritize the most effective ones to attack the root cause of the problem. In this step we make a new measurement to know if the problem was, in fact, solved.
• Control (Control)
Control is nothing more than monitoring the results and ensuring that the improvement is continuous and enduring. Establish control
mechanisms and make the necessary adjustments to the procedures to formalize the changes made.
• Conclusion and evaluation
Upon completing the content seen in the training, you will be challenged to test your knowledge in a final assessment.